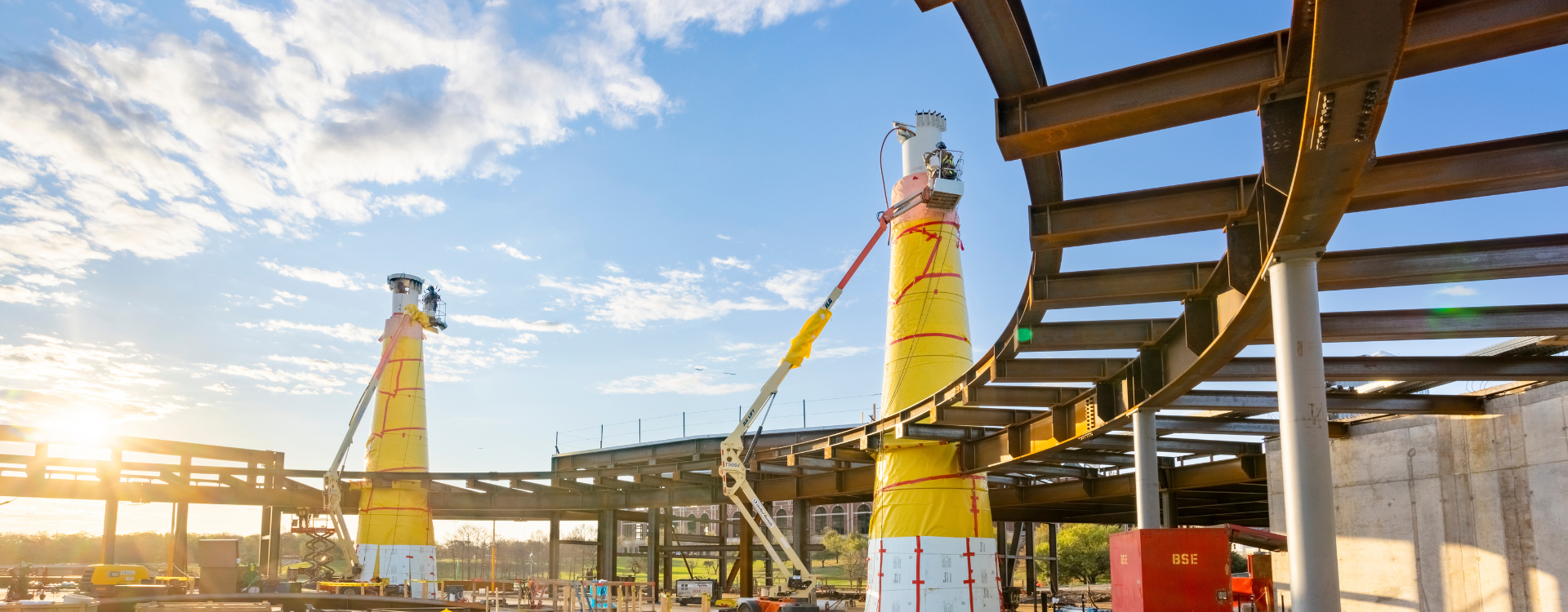
The Challenge
Fitting mechanical, electrical, and plumbing (MEP) systems into The National Medal of Honor Museum's towering concrete columns posed a significant engineering, design, and MEP fabrication challenge. These 5 massive columns, symbolizing the branches of the U.S. military, support a 200-foot by 200-foot steel structure suspended 54 feet above the rotunda. However, there were severe space constraints inside the columns.
"With the top of the columns measuring just 30 inches and two windows of 12 by 24 inches for our utilities to exit into the soffit area, coordinating the exact location of each riser had to be spot on. If installed off by fractions of an inch, the elbows and bends needed to exit would probably clash and installation would be more difficult," Doug Johns, Senior Project Manager, said.
Innovation through Fabrication – The 'Aha' Moment
Success required early collaboration, advanced modeling, and innovative multi-trade racks. From the start, our construction technology team worked closely with engineers and the general contractor to develop a solution that maximized available space.
Using 3D modeling and BIM coordination, we mapped out the exact placement of the MEP systems, ensuring risers fit precisely within the confined column space. This detailed installation video demonstrated how the multi-trade racks would be lowered into place.
"It was clear from the start that there was concern about the constructability of these columns. The fact that we could put those worries to bed and ensure the team that we had a good plan for these columns was the reason we won this project. The video model presented during our interview didn't hurt either," Robbie Hedrick, Business Development Manager, shared.
To streamline installation, we prefabricated the 40-foot multi-trade racks at our Dallas fabrication shop, reducing jobsite labor and improving accuracy. Leveraging Victaulic grooved pipe joining solutions minimized the mechanical footprint and accelerated installation by eliminating the need for complex onsite connections.
"We pride ourselves on empowering our partners to find innovative solutions to complex construction challenges for faster, safer, and easier installations, as demonstrated on impactful projects like the National Medal of Honor Museum," Nick Stason, Regional Manager at Victaulic, said.
Precise field execution was critical. The superintendent went 60 feet into the air to mark exit points, ensuring accuracy before installation. Weeks of coordination with the general contractor, crane operator, safety team, and field crew led to a flawless execution.
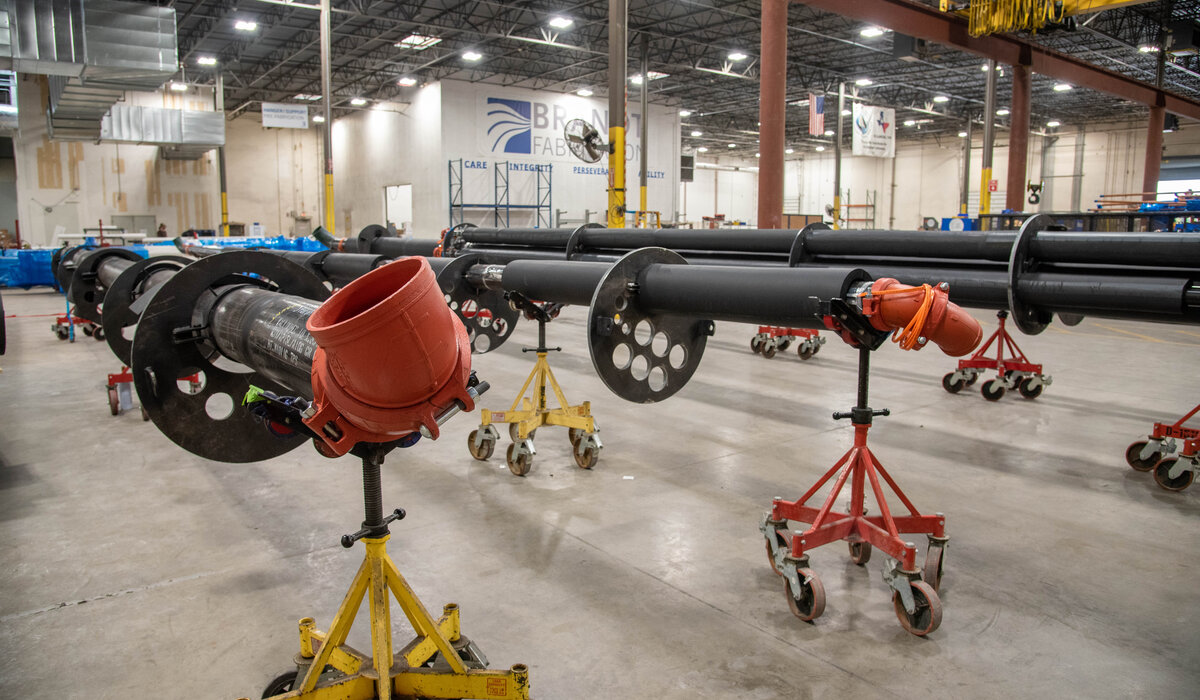
MEP systems being installed in multi-trade racks at our Dallas fabrication shop
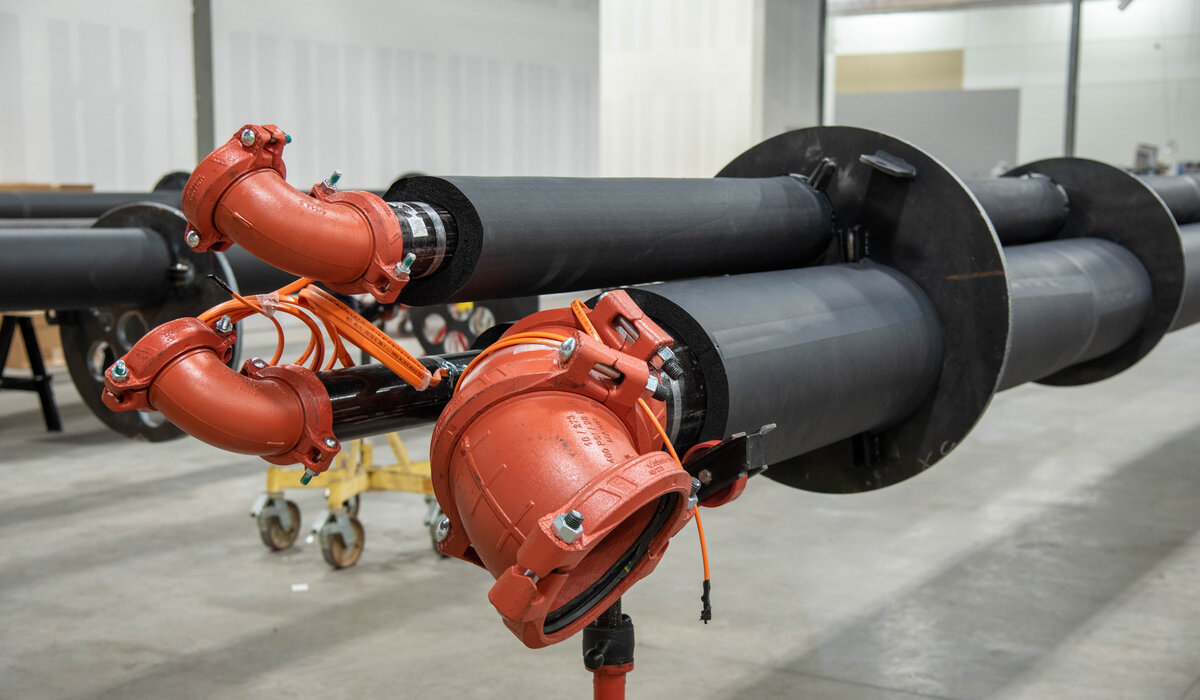
MEP fabrication waiting to be shipped to the jobsite
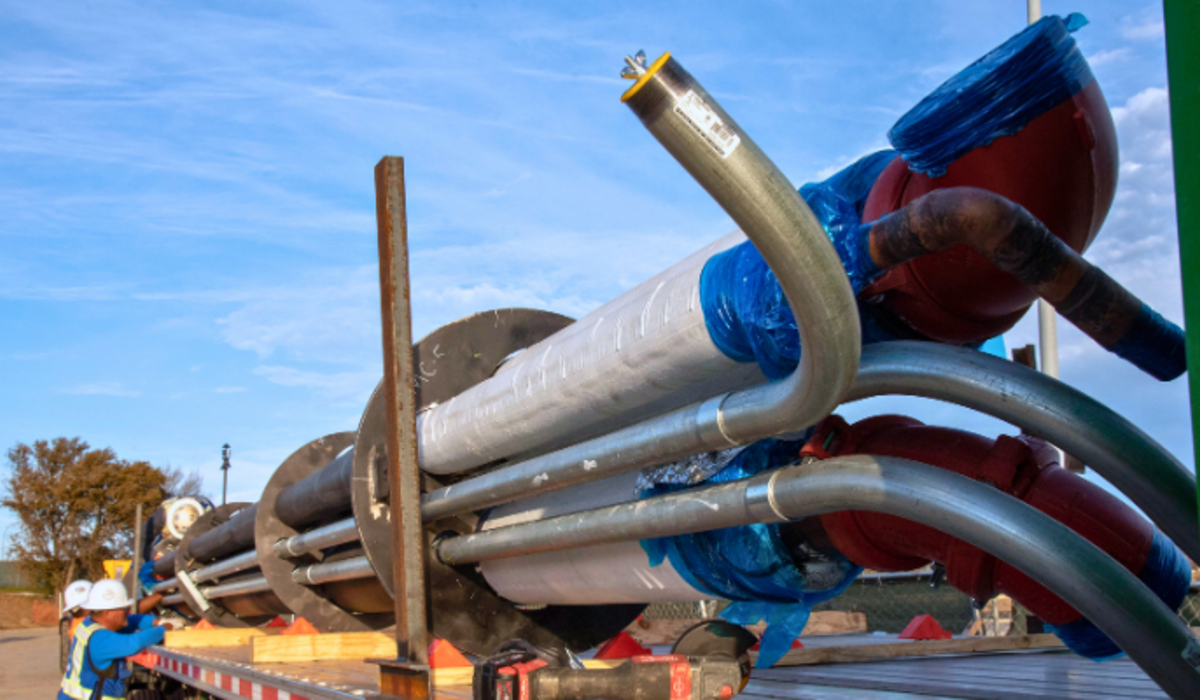
Multi-trade racks arriving on the jobsite
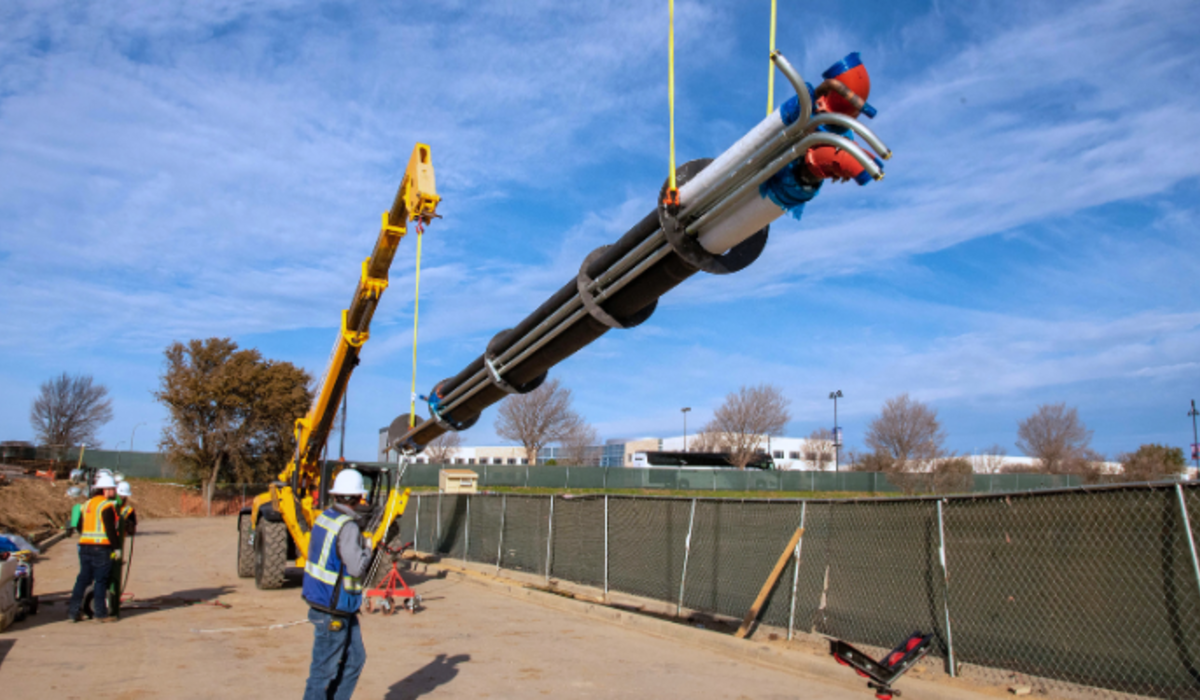
A multi-trade rack being loaded off the truck at the jobsite
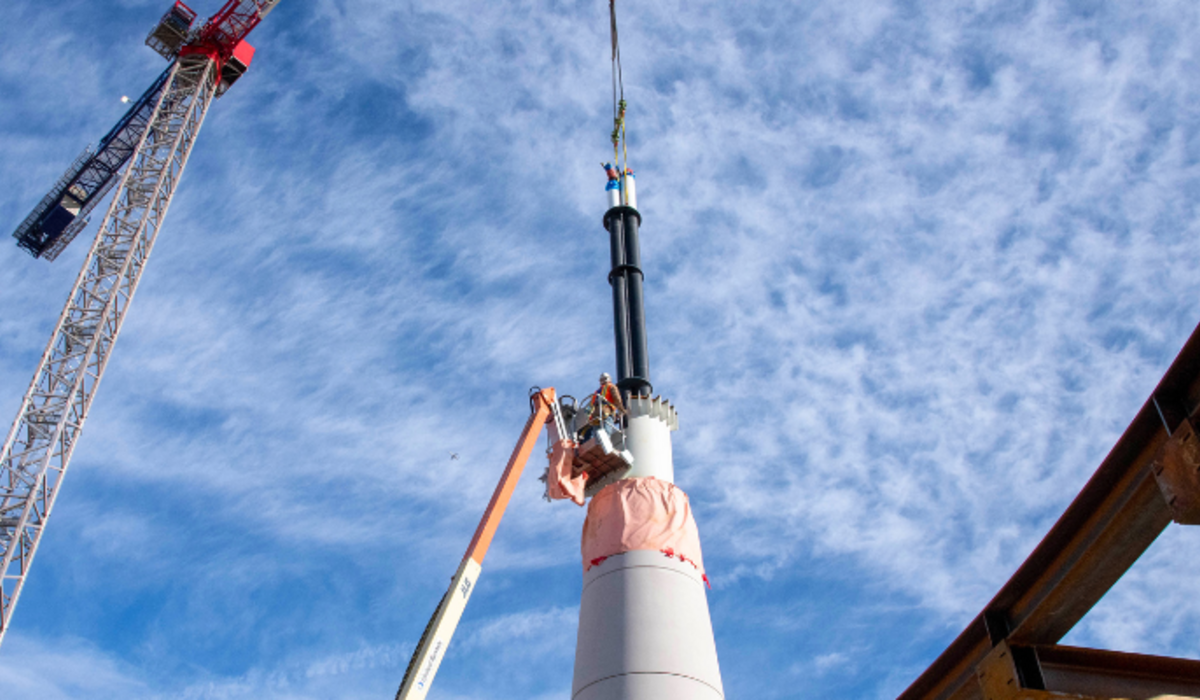
MEP fabrication being installed using a crane
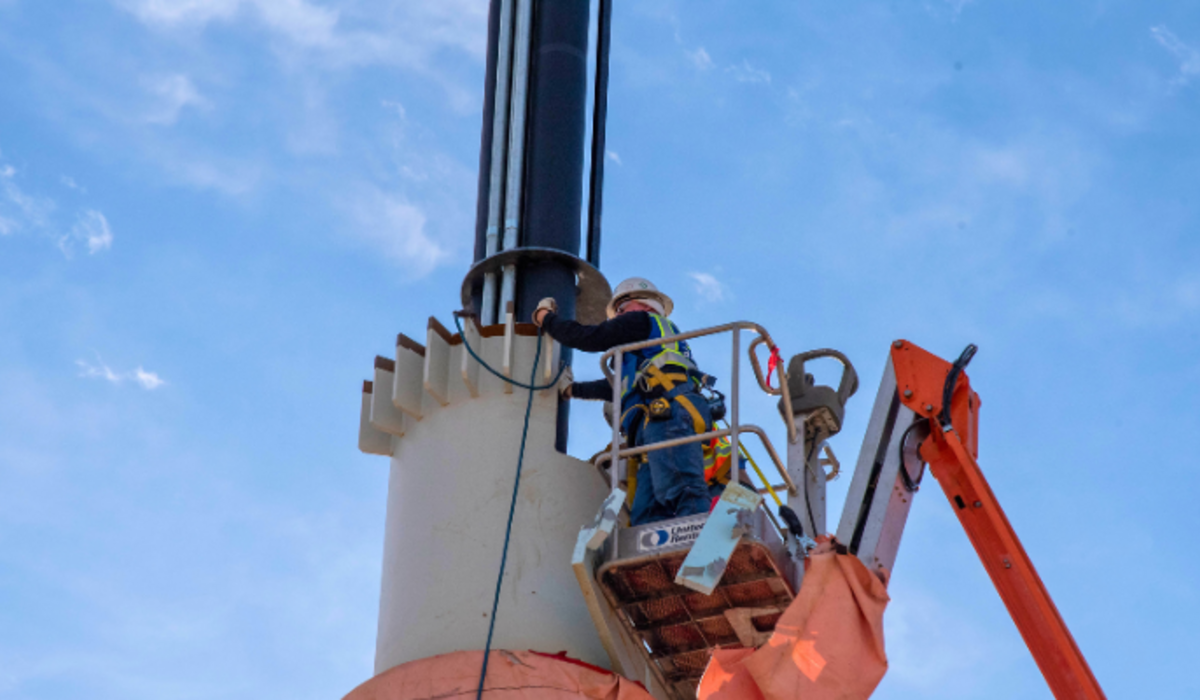
Field employee installing one of the five multi-trade racks
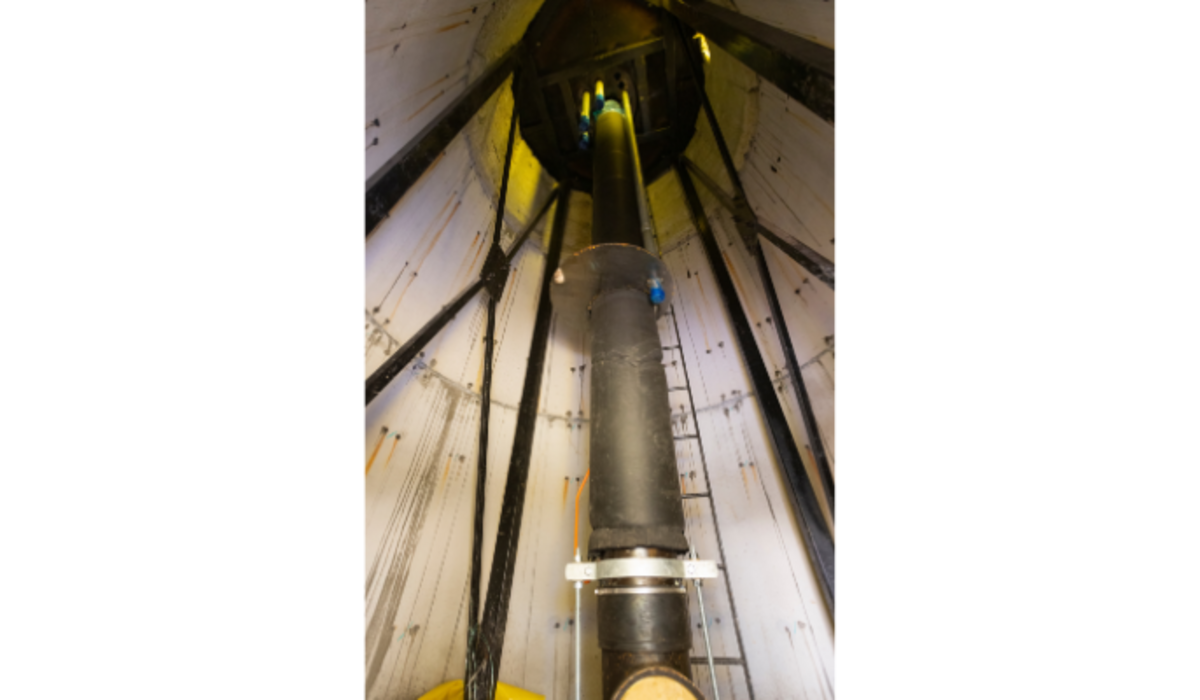
Finished installation of the MEP systems inside the columns
The Bottom Line
By combining advanced modeling with prefabrication, we pushed the boundaries of multi-trade prefabrication in a highly constrained environment. The ability to prefabricate and install MEP systems within such tight spatial constraints streamlined construction while improving quality and safety.
"Our team worked together to provide a solution which resulted in highlighting our capabilities as a full-service MEP contractor," Mike Clarke, Fabrication Director, said.
This approach ultimately provided the customer with a well-coordinated, high-quality system that met stringent design requirements while maintaining the integrity of the museum's structural elements.
We are honored to work on this meaningful project, especially as an employer of veterans and active military personnel. We're proud to support those who have served our country and to contribute to projects that honor their dedication and sacrifice.
Senior Content Marketing Strategist
As Senior Content Marketing Strategist, Lindsay Janssen manages our content lifecycle. From ideation, creation, and editing through distribution, measurement, and maintenance, and creating a content strategy, she develops new and innovative ideas for our digital marketing channels.
Related Reading
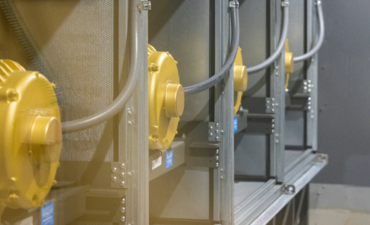
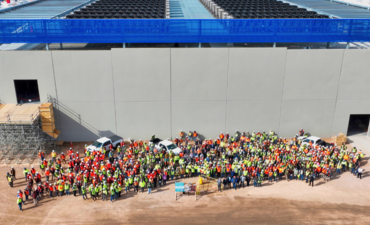
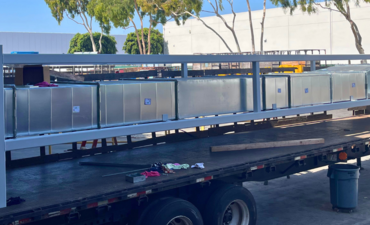