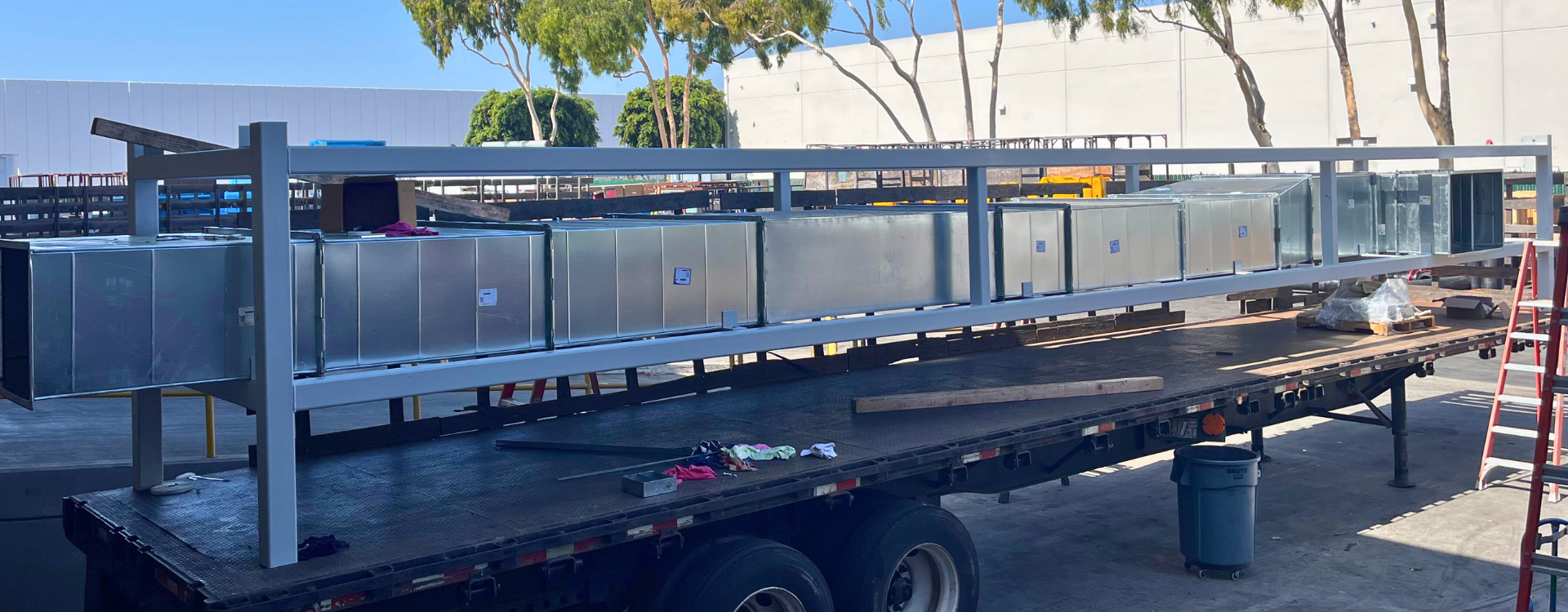
The Challenge
Fabrication for large-scale projects requires precision to maintain quality and efficiency and ensure seamless field installation. On the Social Action Community (SAC) Health – Brier Campus project, our Southern California Division was challenged to reduce labor-intensive assembly onsite while maintaining the quality required in a healthcare environment.
For hospitals specifically, "We have to be more focused on quality rather than quantity," Frederick Cabahug, General Foreman, said. "Being more careful with what goes in the duct's airstream," is critical, especially when working with specialized materials like PolyArmor duct liner insulation, which proved difficult to cut and install due to its foil back layer with thin wires.
Like in any construction project, efficient coordination between fabrication and field teams is crucial. Before implementing Stratus, teams relied on 2D prints, which could potentially lead to inefficiencies and miscommunication. Erik Lopez, Foreman, explained, "Going from a 2D physical paper to Stratus where you have a 3D model has been a game changer. Not only does it eliminate many questions a 2D print brought, but it also allows everyone involved to communicate through Stratus without communicating with them."
Innovation through Necessity - The 'Aha' Moment
Our fabrication team identified an opportunity to preassemble ductwork in-house to streamline the field installation. This approach saved significant labor hours and minimized jobsite safety risks.
"The racked duct we built was unique because everything was built and assembled into one piece at the shop," Fred said. "It saved the field crew lots of labor hours, otherwise it would have been four individuals for three to four days to install and build on the roof." Pre-assembling also reduced the potential for roof damage, a common issue when piecing ductwork together onsite.
By leveraging Stratus, the team optimized fabrication planning and prevented miscommunication. "We were able to use 3D models to section the ductwork together correctly, minimizing questions and errors," Fred shared. The technology allowed the foreman to track fabrication progress in real time, ensuring on-time delivery and installation.
Early in the project, our Southern California Division explored best practices for rooftop duct installation and adopted a proven approach from our Northern California Division to improve water runoff management. Just as the workload is managed and supported across our fabrication network, lessons learned and best practices like these are shared nationwide to drive innovation.
"For roof duct, you can pitch the duct, cross break it, or use other methods to ensure water slides off when it rains," Erik explained. Instead of applying a slope to the entire duct, the team opted to pitch only the center of each top piece. This duct pitching technique proved to be more efficient and effective than traditional methods, reducing the risk of water-related damage. "It just takes a bit more planning and communication," Erik added.
The Bottom Line
This project's fabrication-first approach streamlined installation, reduced labor hours, and improved quality control. By pre-building duct racks, the team eliminated unnecessary fieldwork, minimized installation risks, and ensured accuracy from the start.
"In-house fabrication is critical because we're liable for building it properly," Fred shared. "We can hold ourselves accountable. We can't do that with outside contractors."
Looking ahead, our teams nationwide continue to push the boundaries of fabrication efficiency. "If you can draw it, we can make it," Erik said.
Senior Content Marketing Strategist
As Senior Content Marketing Strategist, Lindsay Janssen manages our content lifecycle. From ideation, creation, and editing through distribution, measurement, and maintenance, and creating a content strategy, she develops new and innovative ideas for our digital marketing channels.
Related Reading
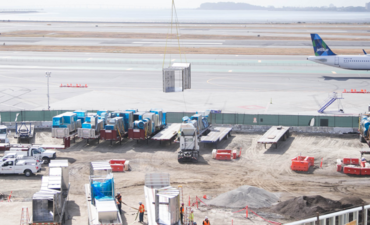
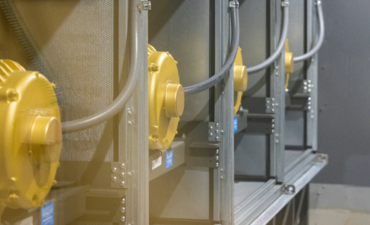
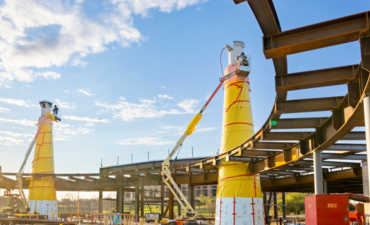