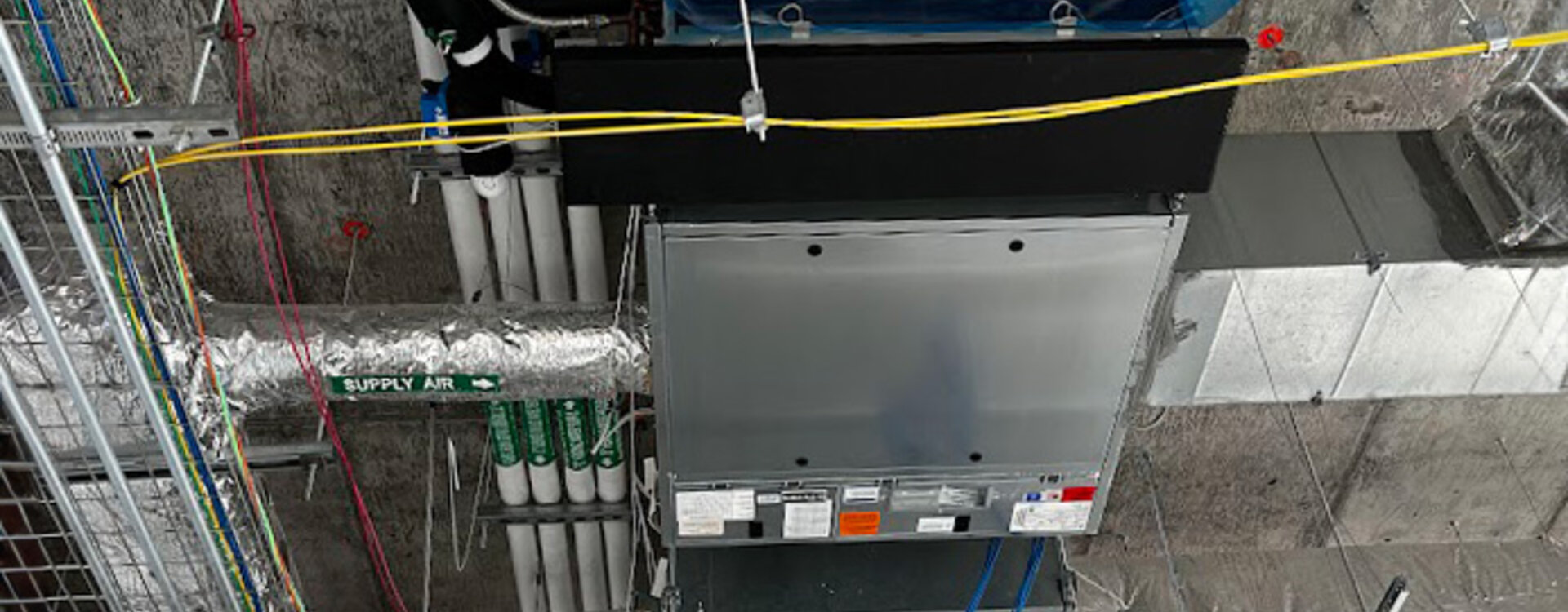
What is a fan powered induction unit?
The term fan powered induction unit — also known as fan powered terminal units with sensible coils, dedicated outdoor air systems, or fan powered terminal units — attempts to define a product that delivers sensible cooling to occupied zones. Like all HVAC equipment, there is a time and place for everything, and sensible cooling terminal units are no exception.
I, personally, see this product as an extension of sensible cooling in general. Starting with chilled slabs or ceilings that deliver relatively low capacity and moving up to active chilled beams with a four to one induction ratio conditioning typical office spaces, then fan powered units delivering higher capacities are for owners that may not know what is going into their space.
This equipment can be purchased from most variable air volume (VAV) fan powered box manufacturers. The conventional series and parallel fan powered boxes are the framework for the sensible unit, with two differences noted from a manufacturer's point of view: first, the primary air inlet typically delivers ventilation air and handles latent loads in the space. Second, a cooling coil is located on the units' induced air inlet either with or without heating capabilities. Though these variances begin to explain a manufacturer's point of view, they do not fully cover the range of issues found in the field during start-up of the equipment.
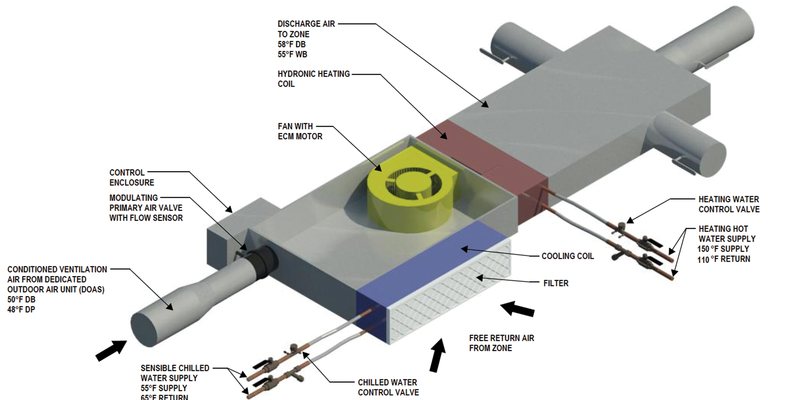
Designing a fan powered VAV box
From an engineer's point of view, there are 10 to 15 unique design options depending on how they are grouped. My two favorites are the following:
- Sensible chilled water temperatures: Each engineering firm has a different opinion about DOAS discharge temperatures, which impacts the sensible coil water supply dewpoint, resulting unit supply air temperature and overall capacity. This psychrometric dance impacts the use of the sensible loop for other loads, such as chilled beams or computer room equipment, and will help define options for winter water side economizers.
- Building automation system controller: This will more than likely be a turbo charged version of the standard VAV box controller — a custom programmable advanced application controller (AAD) in lieu of a VAV box application specific controller with minimal setup. Remember, that we have an ECM motor with modulation capabilities, a cooling coil, modulating control valve(s), and possibly humidistat and dew point calculations. None of those reside with standard VAV equipment, which often surprises owners when they receive final bids. To better understand the control prices, owners should equate the system controls architecture to fan coils or small air handlers, versus VAV.
Basically, we are rediscovering the science behind the original floor mounted induction units sporting low primary airflows with sensible cooling coils in the space.
This vintage equipment functioned with inaccurate pneumatic controls because a solid psychrometric analysis is like gravity — It works every time. The moral of the story is that fan powered induction unit manufacturers' literature provides only part of the story, as the entire system still needs to be fully engineered to operate correctly with the central plant and building itself.
What is a Fan Powered Induction Unit?
Watch MoreVice President
As Vice President, Scott Winkler is responsible for the planning and design of mechanical systems for clients throughout a variety of industries. He maintains certifications in crime prevention through environmental design, plumbing engineering, and energy management.