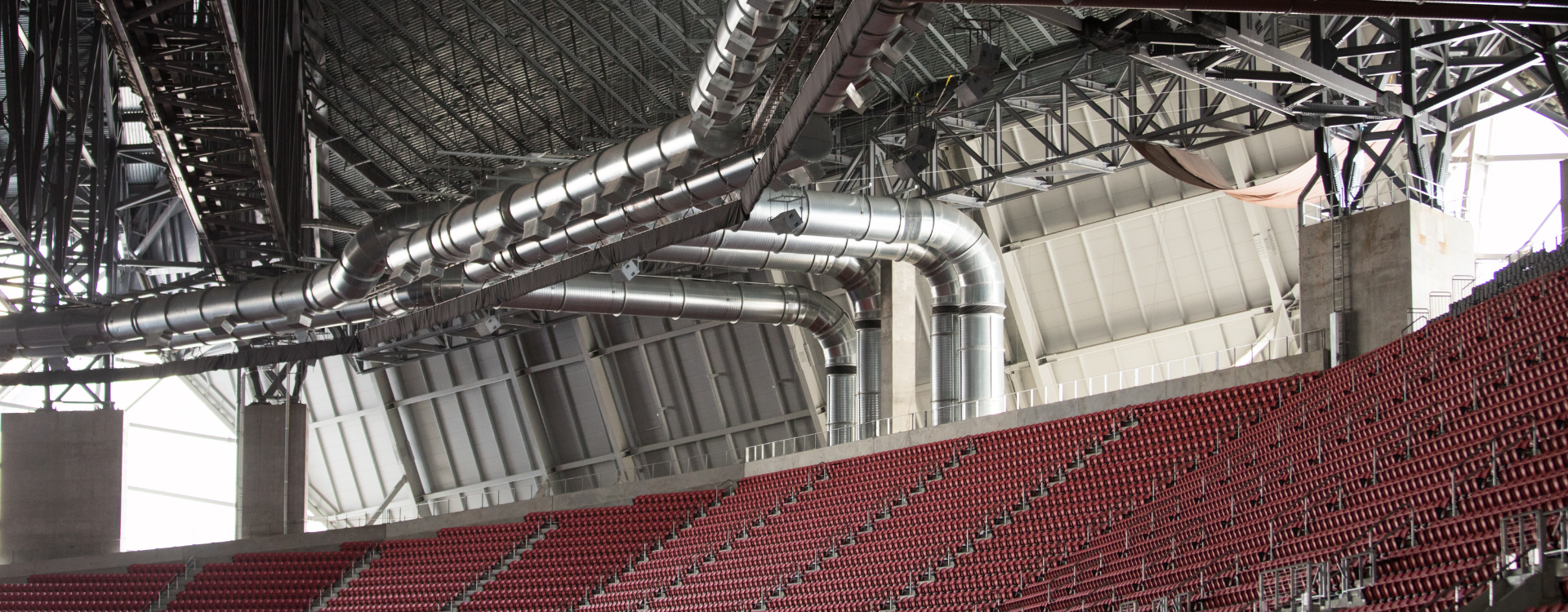
When it comes to stadium projects, no two are alike. With owners seeking a one-of-a-kind facility that delivers an exceptional experience for fans, architectural features, design innovations, and unique building systems help create such spaces, but they also introduce construction challenges and safety hazards. Addressing these safety challenges on complex stadium projects requires additional planning, training, and specialized equipment to ensure the safety of field personnel. From working at dangerous heights to navigating tight spaces, here are some ways to overcome these hazards and ensure employees return home safely each night.
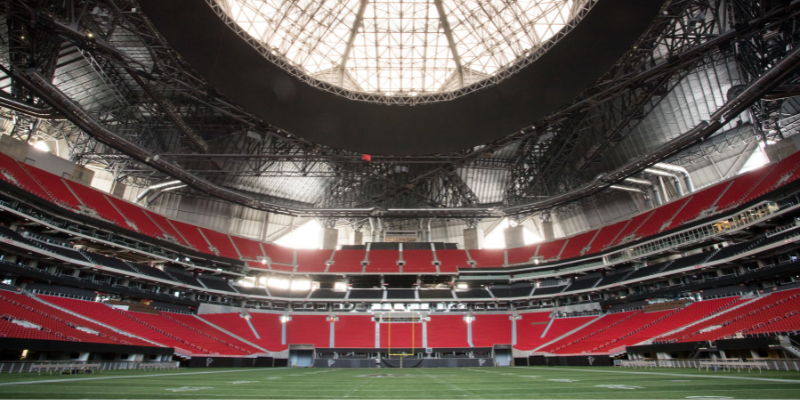
The top five safety and construction hazards on stadium projects are:
Dangerous heights
Stadium projects often involve tasks that require personnel to work at significant heights. For example, if working at a height of 300 feet, this level of work necessitates a safety redundancy beyond conventional fall protection practices. While standard fall protection training is required, working at such extreme heights necessitates additional expertise. Personnel on these projects must complete specialized training and obtain certification from the Society of Professional Rope Access Technicians.
Electrical hazards
Electrical hazards are common on most construction projects, but stadiums pose unique challenges, such as high-voltage rooms in less conspicuous areas. Working in exposed and live high-voltage areas requires extensive training and the use of personal protective equipment, such as arc flash suits, to ensure worker safety. Adherence to guidelines, such as the National Fire Protection Association (NFPA) 70E codes, helps protect all personnel.
Ergonomics
Ergonomic hazards are often overlooked, but they are a significant concern on stadium projects. Despite the large, open nature of these projects, employees frequently work in tight spaces and uncomfortable positions. To address this, implementing a stretch and flex program can help reduce the risk of injury while working in confined areas.
Struck-by and caught-in or between
With numerous activities and personnel working on a single project, equipment and machinery are constantly in use. This increases the risk of workers being struck by or caught in or between machinery. To mitigate this, implement strict speed limits and use spotters to ensure the safety of others during equipment movement. However, even with these precautions, accidents can still occur.
Working overhead
Tight schedules often require separate teams to work simultaneously in the same area, leading to one team working directly above another. This hazard necessitates careful work coordination. Vigilantly coordinating tasks ensures that each trade can perform its work safely without endangering others.
Large projects like stadiums require extensive coordination. Without pre-planning and scheduling, mistakes can lead to incidents, accidents, and near-misses. To address this, it's imperative to streamline schedules and resolve issues before they escalate. Tools such as pre-task plans, job hazard analysis, and committee meetings can be used to minimize daily conflicts and ensure a safe working environment.
Ensuring a safe environment
Mistakes are inevitable, and despite the daily challenges crews face, teams across the industry must create a safe environment for every trade involved when working on stadium projects.
This article was written by a Southland Industries team member.