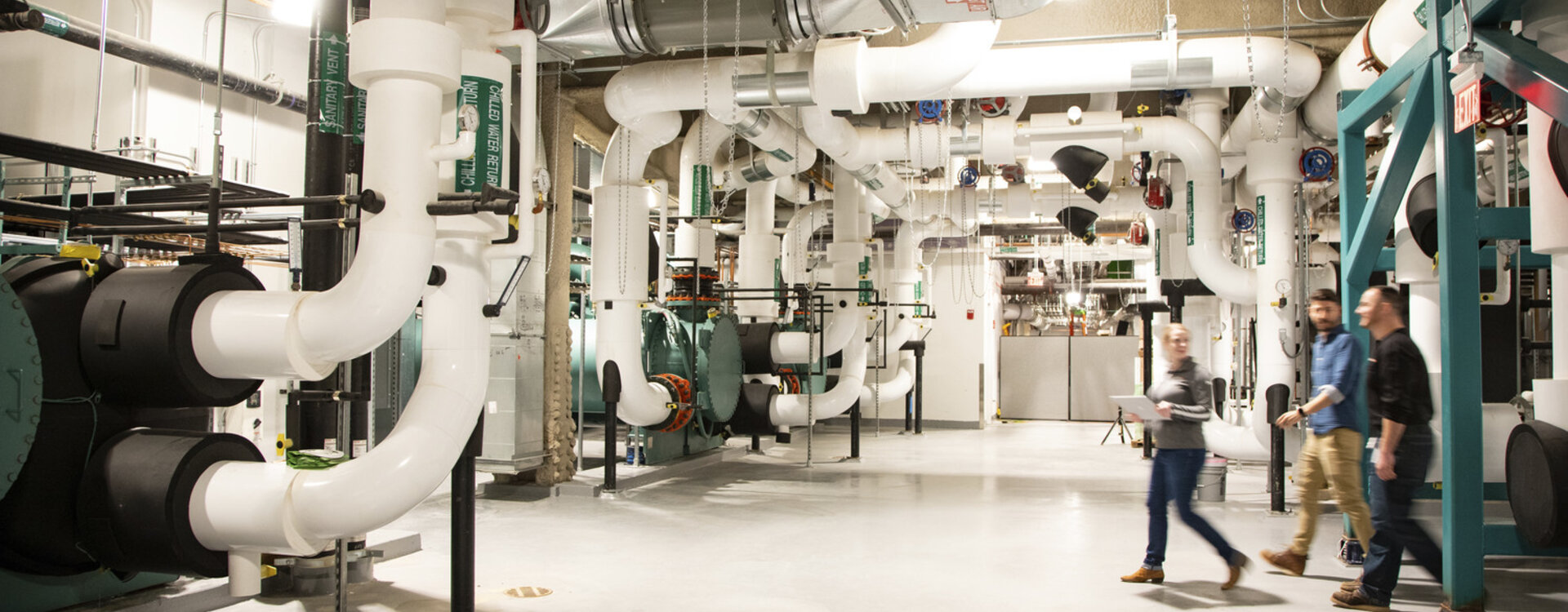
During the colder months, it's imperative to take necessary preventative maintenance steps to keep facilities running smoothly. These essential tips will provide insight on how to properly winterize a facility to ensure it stays safe, comfortable, and efficient throughout the winter season.
Winterization tips for facility managers
1. Begin Preparation Before the First Frost
Start winterization preparations during late fall, before the first frost arrives. Early preparation prevents last-minute scrambling and ensures comprehensive coverage of all systems.
2. Prepare Systems Regardless of Climate
Prepare your facility's maintenance systems for winter, even if you live in a location that doesn't typically experience harsh winters. Unexpected weather events can still occur, such as ice storms, dropping temperatures, windstorms, and rain. Proactive winterization minimizes the risk of emergency repairs, reduces downtime, and extends the lifespan of your systems. It's better to be prepared for any potential winter challenges, ensuring the safety, efficiency, and uninterrupted operation of your facility. To stay proactive, use weather monitoring tools or services to get alerts about sudden weather changes.
3. Monitor for Signs of Problems
Here are some common signs and symptoms that indicate your facility's maintenance systems may need professional attention before winter sets in:
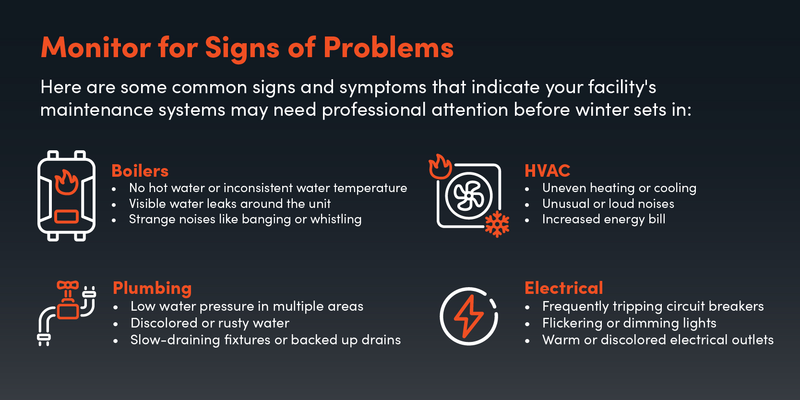
4. Establish a Building Plan
By assessing the status of your systems, you will be able to determine the vulnerable components and identify critical areas that would be most impacted by inclement weather. Additionally, identifying and sourcing materials to keep on hand and designating a plan outlining a response team will help avoid a last-minute crisis. We recommend creating a winterization checklist for the facility and confirming all the emergency contacts are readily available.
5. Perform Regular Maintenance
Mitigate potential issues before they arise by performing preventative maintenance on systems that need work. Benefits of preventative maintenance include improved efficiency, enhanced reliability and extended lifespan of your systems.
6. Conduct Pre-Freeze Audit on Building Systems
Before entering the winter months, conduct a pre-freeze audit to assess the strength of your system. As a facility manager, you can perform several critical inspections before winter arrives:
- Plumbing systems: Locate and identify all isolation valves and their functions. Verify brass fitting protection and prepare to keep water running during sustained cold conditions.
- Domestic water: Map isolation valve locations and cover wall hose bibs. Check insulation adequacy and verify heat trace operation if present.
- Drains: Identify exposed drain lines, particularly in parking garage areas. Plan to shut down condensation-producing units like ice machines during extreme cold.
- Gas: Learn emergency shutoff procedures for gas lines and systems. Check meters for moisture and know proper wrapping procedures for cold conditions.
- Chilled water: If not in use, prepare for system isolation and drainage. Check building automation system settings for low-temperature protocols.
- Unit heaters: Conduct visual inspections of mechanical room and warehouse heaters. Test operation before cold weather arrives.
- Fire lines: Review city guidelines and understand local regulations for cold weather operation.
7. Perform Specific Maintenance Tasks
Certain tasks should be performed by a professional technician to ensure the reliability of your facility's systems throughout winter. These include:
- Boilers: Boiler technicians must perform comprehensive safety checks including low water cut-offs, gas valves, linkage, and operating limits testing. They conduct gas train leak tests and ensure proper carbon monoxide detection. For outdoor boilers, technicians install heat trace systems and rugged insulation for subfreezing protection.
- Electrical: Licensed electricians should conduct IR scanning of critical components, verify torque specifications, and clean electrical systems prone to interruption. They must certify backup power systems and ensure fuel system integrity.
- HVAC: Professionals are needed for direct expansion (DX) system maintenance, including rooftop unit inspection and heat pump servicing. They verify damper operation and prevent ice buildup damage to condenser fan motors.
- Plumbing: Experts can verify backflow device protection, install specialized heat trace systems, and ensure compliance with fire suppression regulations. They're essential for implementing proper drainage protocols and installing advanced freeze protection measures.
8. Optimize Performance of Heating Systems
Heating systems should undergo regular maintenance, and programmable thermostats should be utilized to automatically adjust temperature settings based on occupancy and time of day. Divide the facility into different zones with separate thermostats and upgrade aging heating equipment to newer, more efficient models. Seal any leaks or air gaps around windows, doors, and other openings to prevent drafts and heat loss, insulate exposed heating pipes, and utilize energy-efficient upgrades. To prevent moisture buildup which could lead to mold or discomfort, use humidity controls on your HVAC system and use dehumidifiers in areas that tend to get too damp.
Through proactive planning and maintenance, facilities can be properly winterized to ensure the safety, comfort, and efficiency of operations throughout the winter months.
Senior Sales Account Consultant
As Senior Sales Account Consultant, Ryan fosters proactive and seamless communication between all parties to ensure exceptional service delivery. He secures new and ongoing work for our service team by establishing and maintaining contact with existing accounts and potential clients for commercial and industrial maintenance and repair services.