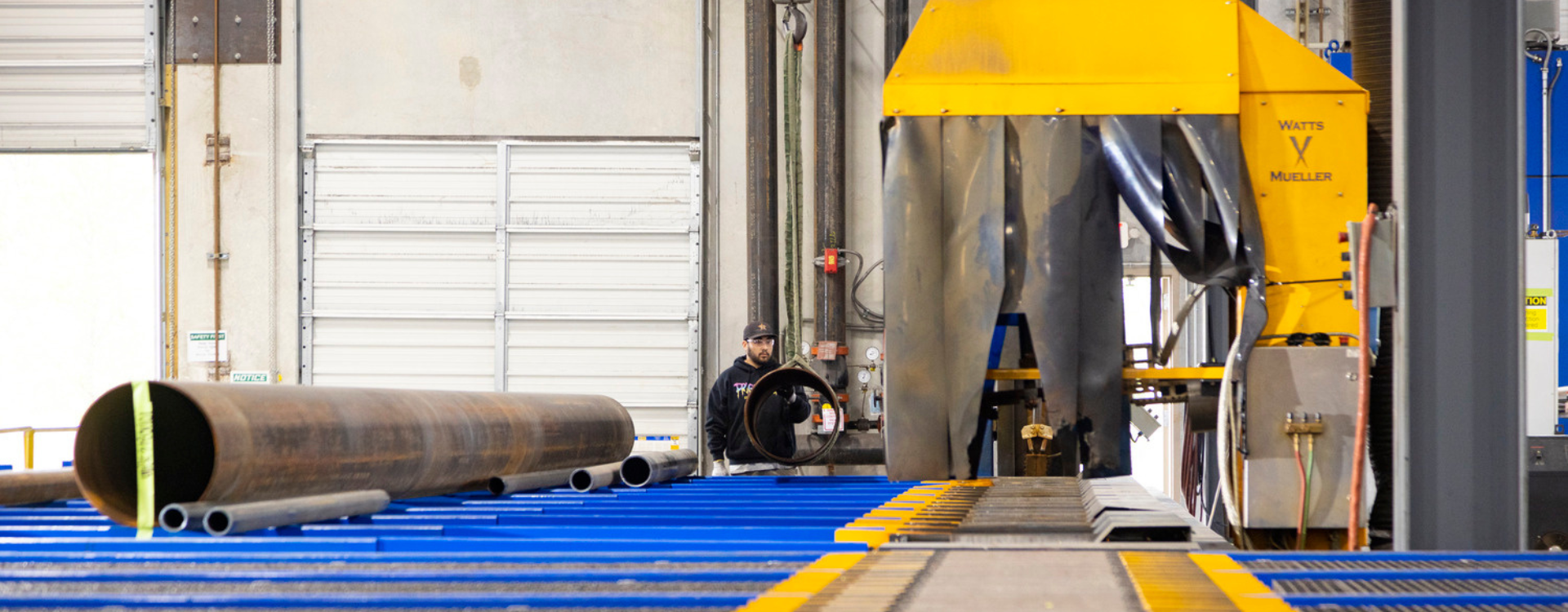
While prefabrication continues to prove it is the future of the AEC industry, national contractors must utilize standardized software across fabrication shops to ensure consistent training and facilitate workload sharing across regions.
Southland has become the first organization to complete a PypeServer fabrication piping software retrofit on its existing piping profiler machines across two fabrication shops in Texas and Pennsylvania. This achievement was made possible through the leadership of Justin Spears, Senior Fabrication Technology Analyst, who worked closely with our fabrication shop leads, including Robert Jones, Fabrication Director, who oversees our San Antonio fabrication shop, and Michael Jones, Foreman, who oversees our Philadelphia fabrication shop, to implement this technology change.
What is PypeServer software?
PypeServer software is an advanced software solution designed for use in the piping industry, particularly for managing and optimizing the cutting and fabrication of pipes. It integrates with various types of pipe profiling machines to streamline operations, enhance precision, and improve overall efficiency.
"Prior to the retrofit, four of Southland's fleet of seven pipe profilers were running PypeServer software. Following the retrofit, all of them are," David Basiji, PypeServer CEO, said.
What is fabrication piping software?
Fabrication piping software is an advanced software solution designed for use in the piping industry, particularly for managing and optimizing the cutting and fabrication of pipes. It integrates with various types of pipe profiling machines to streamline operations, enhance precision, and improve overall efficiency.
Southland's piping profilers are advanced multi-axis computer-controlled pipe cutting machines equipped with a precision profiling carriage on precision-engineered rails. These machines provide simultaneous 3D torch motion to maintain cutting precision both along the pipe's linear axis and perpendicular to it, enabling precise beveled holes and end cuts. They are highly effective in achieving clean cuts, bevels, o-lets and saddles on 2.5-inch and larger diameter pipes that can be over 40 feet long.
"Southland incorporated PypeServer on our piping profiler machines in all divisions to consolidate the types of software we support, have consistent and standardized training, and facilitate troubleshooting. By standardizing, we are more agile in making changes within our projects and sharing work amongst each division to get the work done quicker and more consistently," shared Justin.
How to approach a fabrication piping software retrofit
There are several moving parts to accomplish a fabrication software retrofit within a piping profiler machine. Our AEC technology team approached the retrofit following the below steps:
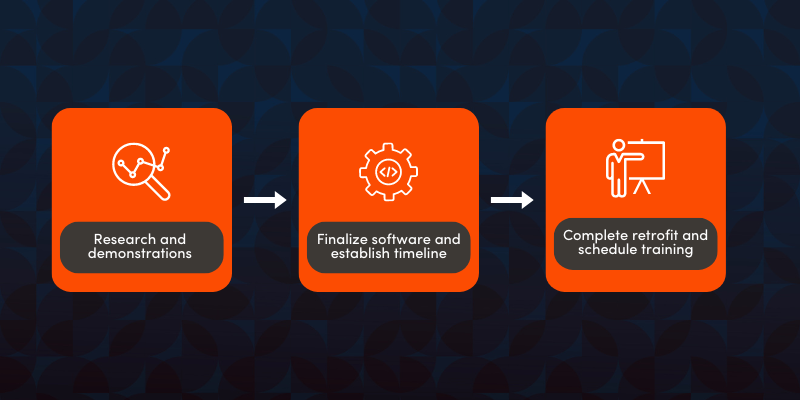
Research and demonstrations
Researching the existing software offerings within the AEC industry was essential. We thoroughly compared target products and evaluated their suitability forour company's needs. Once our team identified preferred options, they requested a detailed demonstration to assess their advantages and disadvantages.
Finalize software and establish timeline
We determined which software suited the organization's needs based on the findings. From there, we met with key stakeholders to finalize the retrofit process to facilitate a seamless transition.
“The process involved obtaining quotes, cost approval, scheduling the shops downtime for minimal impact on productivity and coordinating the delivery of necessary parts to install new controls and computers,” Justin said.
Complete retrofit and schedule training
Our team completed the retrofit during an established week timeline. The retrofit included replacing all existing controls, computers, and wiring with new components to optimize the setup. Following installation, the piping profiler underwent meticulous calibration and servicing to ensure adherence to factory standards. Once completed, we scheduled comprehensive training sessions with the machine operators and fabrication shop leads to enhance proficiency and boost overall productivity.
Challenges with the fabrication software retrofits
During the retrofits in our fabrication shops, we faced several challenges, notably inconsistent parts and unforeseen issues with machines.
Encoder
Encoders convert motion to an electrical signal that a control device can read. We ordered the correct encoder part during the retrofit in the Philadelphia fabrication shop to account for the inconsistent parts and ensure accurate calibration. This challenge allowed us to be proactive during our San Antonio retrofit project.
Motor driver
During the retrofit in San Antonio, we discovered a motor driver that was too low voltage to fully operate the motor. "To overcome this issue, we had to ship out the motor to get it dialed into the new system with a new motor drive that could supply the correct voltage to make the motor work properly. Doing this also let the machine go from being able to cut 24-inch pipe to 36-inch pipe, which was a huge upgrade for the shop," Justin said.
Screw assembly
In a Watts machine, the screw assembly is a mechanical component responsible for precise movement and positioning. The screw assembly is crucial for tasks such as positioning the cutting head, adjusting the height, or moving workpieces accurately. We upgraded screw assemblies to have optimized machine efficiency and to facilitate future preventative maintenance.
Benefits of a fabrication technology retrofit
The benefits of a fabrication technology retrofit can be seen immediately through process improvement and fabrication workflow enhancements.
Troubleshooting and training
Implementing the same software infrastructure across all divisions simplified the troubleshooting process for piping profiler machines. PypeServer provides reliable support and incorporates user feedback to enhance diagnostic capabilities. Using the same software, we standardized training and encouraged sharing lessons learned across divisions.
“The retrofit was a vital piece in refining the Philadelphia fabrication shop. Productivity is a way of life,” Michael said.
Quality improvement and reduced waste
Staying up to date on fabrication technology means continually focusing on quality improvement. The software before the retrofit included more manual calculations, specifically during the homing-in process.
"With the previous software, there was a three-foot dead zone that the torch cannot reach between the cutting head carriage and the chuck that holds the pipe. This led to a lot of material waste. The new software recognizes the dead zone and nests a longer part within that length to use every inch of pipe, dramatically reducing waste," Robert said.
Operator experience
The PypeServer software automates the creation of holes for o-lets and saddles at pipe intersections and eliminates the need for manual decimal-to-fraction conversions, while pipe size and wall thickness entry are automated and retained, saving employees time and reducing the risk of errors. This automation improves the efficiency of the fabrication process and enhances the operator's experience.
"Operator experience is much easier and quicker to adapt to the PypeServer software and increases cutting productivity," Justin said.
Future proofing
Southland is working with the team at PypeServer to add custom features that'll facilitate Southland's standardization of fabrication workflow software upstream of the pipe profilers, further adding to fabrication process efficiency.
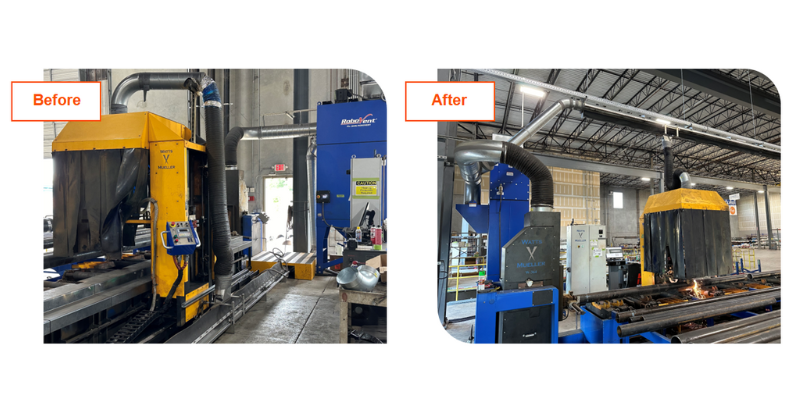
Innovations within AEC technology
Staying at the forefront of fabrication piping software and technology enables differentiation from competitors and can lead to more work. A retrofit, while time-consuming, ensures an organization is on the same page regarding fabrication production.
It is increasingly essential for mechanical and plumbing contractors performing projects across the United States to practice workload sharing across regions. For Southland, resource sharing allows one fabrication shop to assist when another might be overwhelmed with tight construction timelines.
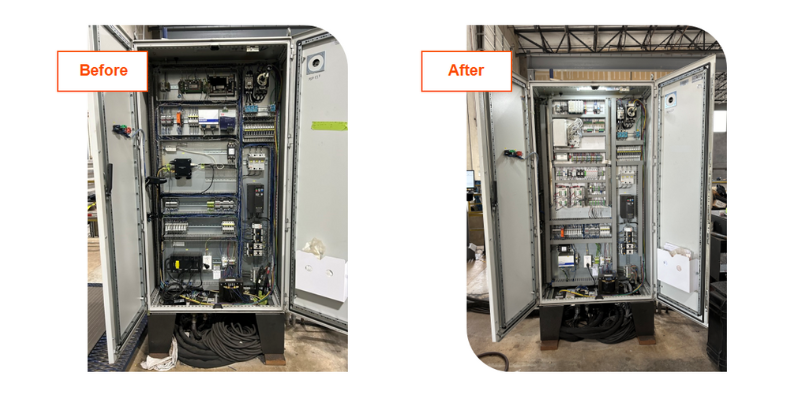
Senior Content Marketing Strategist
As Senior Content Marketing Strategist, Lindsay Janssen manages our content lifecycle. From ideation, creation, and editing through distribution, measurement, and maintenance, and creating a content strategy, she develops new and innovative ideas for our digital marketing channels.