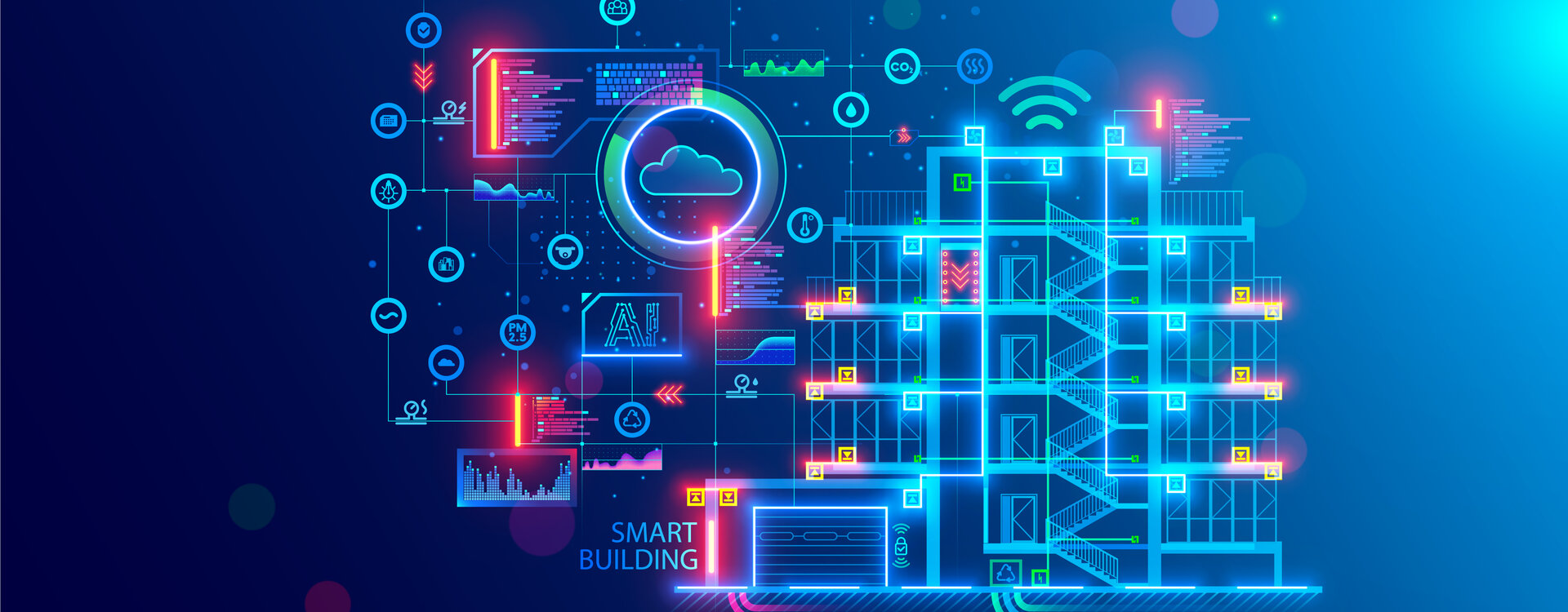
In today's world of facility management, there is an expectation that facility managers need to make timely, business-driven decisions. To do this, they need a more intuitive way to connect facility data with system performance. As facilities become more complex, more automated, and adapt to the ever-changing world, there are no signs of the demand for data slowing down.
Facility teams are turning to more advanced building management systems (BMS) paired with the right analytics software to deliver the data in ways they need to better run their facilities. Plus, the improved Internet of Things (IoT) technology can provide data on demand to the palm of your hand — even if you're offsite.
"Data can be a building owners' most valuable asset to gain insights and make informed business decisions. When it clocks and clients understand how they can leverage their data to tell a story, that inspires actions for a better outcome. The decision to move forward with BMS and analytics upgrades becomes easy." -Jason Gladney, Preconstruction Manager
To run facilities more efficiently while saving time and operating costs, teams can leverage technologies to better diagnose, repair, and maintain their systems with real-time data. Context-based insights on building conditions, assets, and HVAC equipment are clearer than ever before and more clients are making data-driven decisions regarding their HVAC equipment.
With data offering facility managers powerful insights, how is the data driving overall HVAC trends in the industry?
Indoor Air Quality (IAQ) upgrades and improvements
Before 2019, air filtration, airborne pathogens, and disinfectant technology were hardly addressed and were reserved for specific clients. Today, more companies are talking about IAQ and what technologies are available for their space.
As a result of COVID-19, we see clients taking the first step in implementing IAQ upgrades and requesting systems assessment reports specifically for their facility. A BMS can provide IAQ data, not only for airborne pathogens, but also for CO2, gas, and dust. Additionally, emergency repairs or replacements can be avoided when BMS data shows necessary maintenance for HVAC components prior to scheduled services.
Rise in more energy-efficient HVAC systems
Investing in modern, energy-efficient HVAC equipment reduces energy costs and puts less stress on the equipment, extending its useful life expectancy and reducing the building's carbon footprint. The cost-savings produced through the more efficient equipment upgrade can often help offset installation costs.
"During the pandemic, a good percentage of building owners were able to use various forms of relief money to upgrade HVAC systems, which allowed those owners to select more efficient equipment and offset their increased utility consumption. It's in a building owners' best interest to make efficiency upgrades that work in tandem with these upgrades to manage their costs and leverage their available funds in the smartest way possible." -Dominic Cardenas, Senior Account Executive
HVAC systems equipped with the proper sensors can collect real-time data about energy consumption, allowing facility managers to make smarter operational decisions tied to how these systems run. Optimizing a BMS Sequence of Operations (SoP) Program to anticipate and adapt to things such as temperature, airflow levels, humidity, CO2, light levels, and operational schedules, without the need for manual intervention, are just a few ways companies are benefitting from more energy-efficient, data-driven HVAC systems.
Preventative vs. reactive HVAC maintenance
While it's an industry standard that an ideal facility management team always has a preventative maintenance plan in place, better facility data has also made it easier for facility teams to push this through. As BMS technology and smart data analytics advances and diagnostics become more precise, these systems are allowing preventative maintenance measures to be implemented, resulting in maintenance workers and facility teams being less reactive and more efficient in their day-to-day operations.
While unplanned downtime still happens, having a preventative facility maintenance plan largely reduces the need for facility teams to fix issues that could've been previously resolved with real-time facility insights. This means safety measures are improved, and equipment longevity is increased.
Now trending
As the industry continues to be shaped by trends and real-world events, data has proven to be invaluable when making decisions for maintenance and overall facilities management. Without data, decision-making and planning could be made on guesses leading to unpredictable outcomes, but with data, facility managers can make informed, solid decisions for predicted outcomes.
Sales Account Consultant
As Sales Account Consultant, Tyler Meinecke focuses on delivering facility maintenance solutions for new commercial clients and markets within our Southern California Division. His active involvement with the International Facility Management Association (IFMA) and at educational events and seminars within the industry helps him to advise companies regarding their facility maintenance goals.